This university needs thousands of housing units. A factory is building them
With enrollment on the rise, the California Polytechnic State University in seaside San Luis Obispo has found itself staring down a familiar California problem: a severe housing shortage. “Cal Poly’s located in this beautiful town of San Luis Obispo. That is one of our competitive advantages, but it also means that everybody else wants to live here, too,” says Mike McCormick, vice president of facilities management and development at Cal Poly, San Luis Obispo This desirability poses a problem for the university, which has seen enrollment grow in recent years, with trendlines suggesting an additional 4,000 students by the end of the decade. “It’s really hard for us to grow without providing housing,” McCormick says. “The city simply can’t absorb any of it. So that’s what’s driving our program.” That’s led the university to launch an ambitious, fast-paced, and possibly precedent-setting dormitory building project that will add 4,200 beds to the university’s campus housing inventory within just four years. The housing—nine buildings primarily made up of six-bed, three-room suites—will be built through modular construction inside a factory in Los Angeles. It will be the largest modular housing construction project in the country. [Image: courtesy Steinberg Hart Architects] The university partnered with FullStack Modular, a company specializing in industrialized construction that has previously built modular apartment buildings up to 15 stories tall, to produce the much-needed housing units quickly and affordably. Construction will commence later this year at FullStack Modular’s Los Angeles factory, and the first of nine new dormitory buildings is scheduled for occupancy in Fall 2026. FullStack Modular emerged in 2016 after a major 15-building modular construction project connected to the Barclay’s Center arena in Brooklyn faltered. Just one of the project’s buildings, a 32-story tower, was completed. It was, at the time, the tallest modular project in the world. Roger Krulak, an executive who worked on that project, created FullStack Modular and bought out the factory and the production process, and has chipped away at making a market for factory-built buildings ever since. [Image: courtesy Steinberg Hart Architects] As the largest modular construction project in the country, the 4,200-bed project now underway in California represents a high-profile test of the modular approach. It’s also a no-brainer example of how modular construction can be used to pump out a fairly cookie-cutter type of building—thousands of dorm suites—fast and cheap. “We can predict timing and costs and repetitiveness and all of the economies of scale that you hope for in an industrialized process,” says Krulak. [Image: courtesy Steinberg Hart Architects] McCormick says the university was quick to latch onto the idea of factory-based construction for this project. That’s partly due to the lack of construction workers in the area to build a 4,200-bed project, and a lack of space to house workers who might relocate there for such a project. “Using traditional methods, we would import a workforce from Los Angeles, from the Valley, from San Francisco, and they would all be looking for housing while they’re here,” McCormick says. “That just exacerbates the problem that we’re trying to solve in the first place.” Building the project in a factory solves the workforce problem. It also brings the cost of construction down by systematizing the design into repeatable forms. “It doesn’t make sense to build this much housing and not take advantage of the repeatability,” McCormick says. FullStack Modular is currently building a prototype of the six-bed dorm suite that will make up about 80% of the project’s square footage. Krulak says it will be used to fine-tune the design before putting the factory into full production mode later this year. When underway, the process is expected to move twice as fast as conventional construction, and with much greater certainty over material and labor costs. Finding an affordable construction solution is not just a speculative real estate decision. At Cal Poly, and other universities across the country, housing is now more expensive than tuition. Modular housing could prove to be one way to increase supply and reduce costs. “The CSU is the largest university in the country. We have needs for housing all over the place,” McCormick says. “It’s a common problem, especially here in California, so we’re hoping that we create something that is absolutely transportable to other universities.”
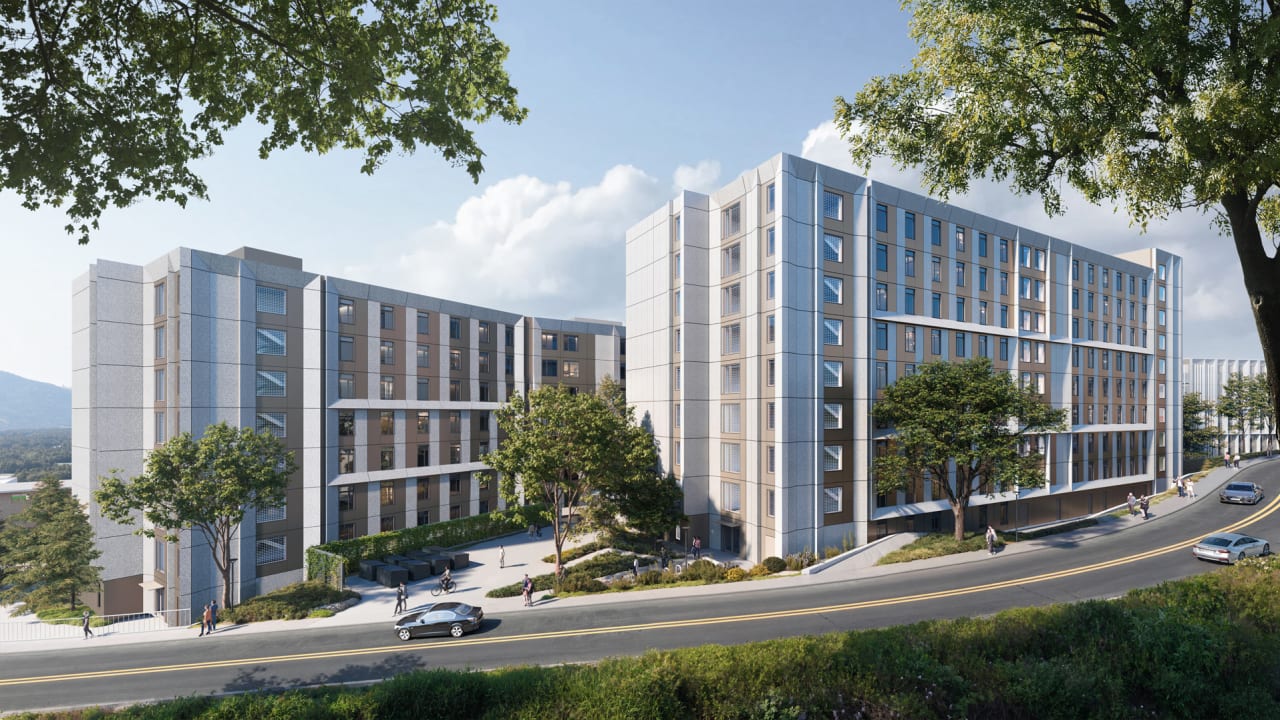
With enrollment on the rise, the California Polytechnic State University in seaside San Luis Obispo has found itself staring down a familiar California problem: a severe housing shortage.
“Cal Poly’s located in this beautiful town of San Luis Obispo. That is one of our competitive advantages, but it also means that everybody else wants to live here, too,” says Mike McCormick, vice president of facilities management and development at Cal Poly, San Luis Obispo
This desirability poses a problem for the university, which has seen enrollment grow in recent years, with trendlines suggesting an additional 4,000 students by the end of the decade. “It’s really hard for us to grow without providing housing,” McCormick says. “The city simply can’t absorb any of it. So that’s what’s driving our program.”
That’s led the university to launch an ambitious, fast-paced, and possibly precedent-setting dormitory building project that will add 4,200 beds to the university’s campus housing inventory within just four years. The housing—nine buildings primarily made up of six-bed, three-room suites—will be built through modular construction inside a factory in Los Angeles. It will be the largest modular housing construction project in the country.
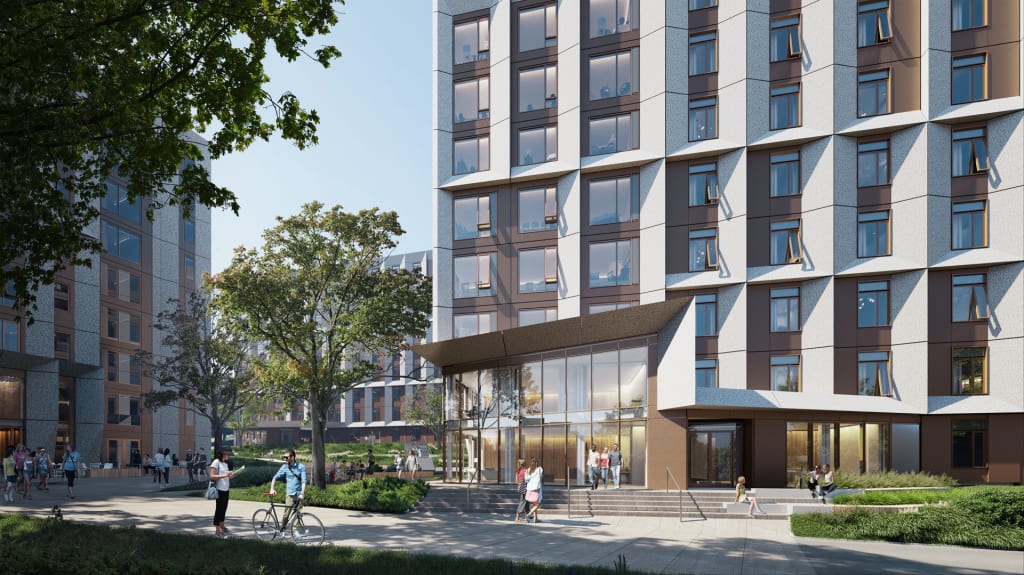
The university partnered with FullStack Modular, a company specializing in industrialized construction that has previously built modular apartment buildings up to 15 stories tall, to produce the much-needed housing units quickly and affordably. Construction will commence later this year at FullStack Modular’s Los Angeles factory, and the first of nine new dormitory buildings is scheduled for occupancy in Fall 2026.
FullStack Modular emerged in 2016 after a major 15-building modular construction project connected to the Barclay’s Center arena in Brooklyn faltered. Just one of the project’s buildings, a 32-story tower, was completed. It was, at the time, the tallest modular project in the world. Roger Krulak, an executive who worked on that project, created FullStack Modular and bought out the factory and the production process, and has chipped away at making a market for factory-built buildings ever since.
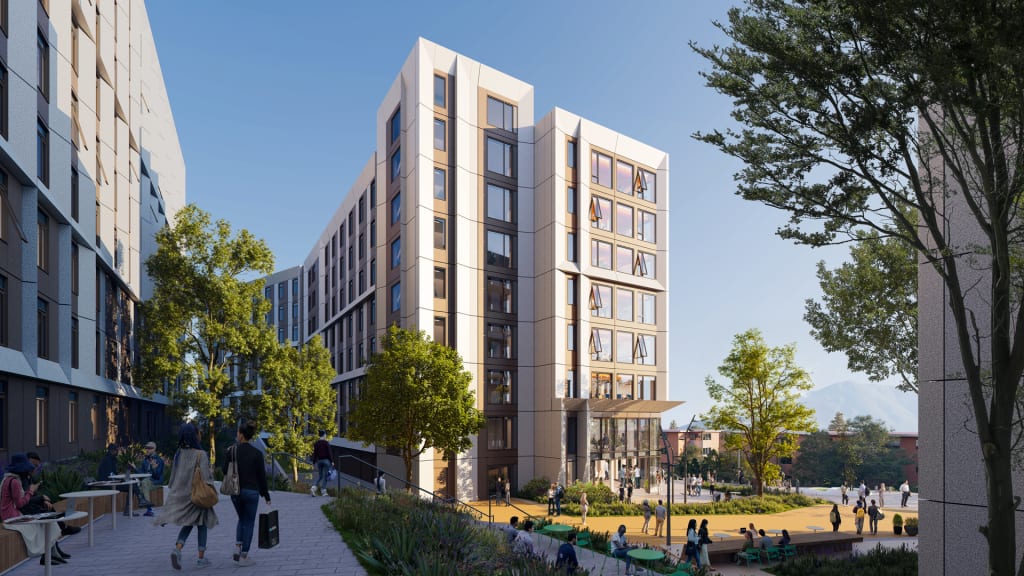
As the largest modular construction project in the country, the 4,200-bed project now underway in California represents a high-profile test of the modular approach. It’s also a no-brainer example of how modular construction can be used to pump out a fairly cookie-cutter type of building—thousands of dorm suites—fast and cheap. “We can predict timing and costs and repetitiveness and all of the economies of scale that you hope for in an industrialized process,” says Krulak.
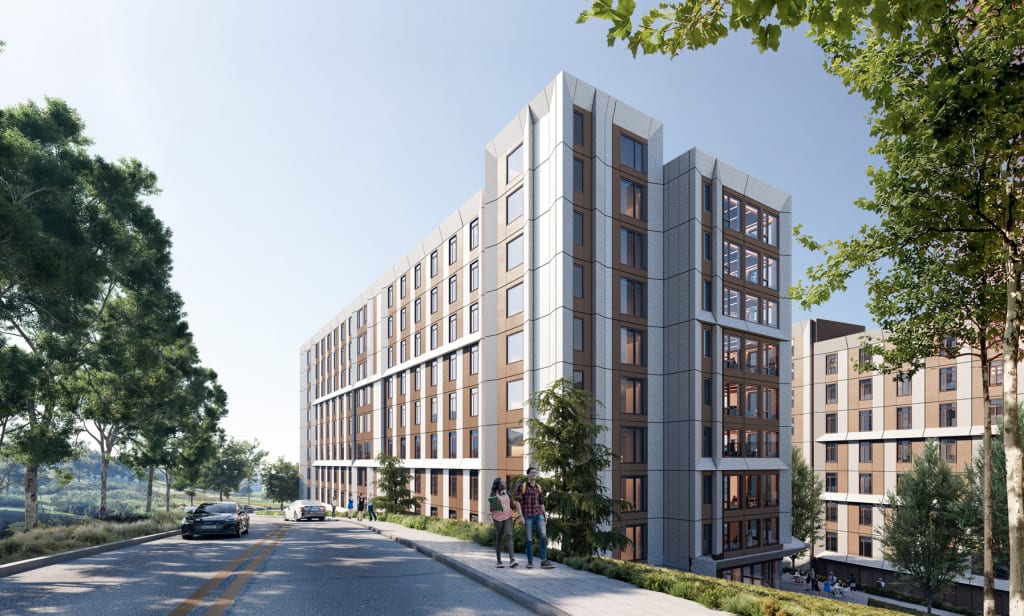
McCormick says the university was quick to latch onto the idea of factory-based construction for this project. That’s partly due to the lack of construction workers in the area to build a 4,200-bed project, and a lack of space to house workers who might relocate there for such a project. “Using traditional methods, we would import a workforce from Los Angeles, from the Valley, from San Francisco, and they would all be looking for housing while they’re here,” McCormick says. “That just exacerbates the problem that we’re trying to solve in the first place.”
Building the project in a factory solves the workforce problem. It also brings the cost of construction down by systematizing the design into repeatable forms. “It doesn’t make sense to build this much housing and not take advantage of the repeatability,” McCormick says.
FullStack Modular is currently building a prototype of the six-bed dorm suite that will make up about 80% of the project’s square footage. Krulak says it will be used to fine-tune the design before putting the factory into full production mode later this year. When underway, the process is expected to move twice as fast as conventional construction, and with much greater certainty over material and labor costs.
Finding an affordable construction solution is not just a speculative real estate decision. At Cal Poly, and other universities across the country, housing is now more expensive than tuition. Modular housing could prove to be one way to increase supply and reduce costs.
“The CSU is the largest university in the country. We have needs for housing all over the place,” McCormick says. “It’s a common problem, especially here in California, so we’re hoping that we create something that is absolutely transportable to other universities.”