This Pittsburgh townhouse is only 16-feet wide but could help solve the housing crisis
On a narrow lot in Pittsburgh, a new building is three stories tall but only about 16 feet wide. The shape is based in part on the constraints of the lot—it’s not uncommon for houses in the city to be very narrow. “When you think about Rust Belt cities, there’s a lot of ‘missing teeth’ lots . . . many of these lots in the city of Pittsburgh are 20 feet wide,” says Dennis Steigerwalt, president of the Housing Innovation Alliance, part of a group that built the home as a model for more sustainable, affordable housing. [Photo: Prep Solutions] There’s another reason for the size: Because the home was built in a factory, it also meant that each module couldn’t be wider than 16 feet in order to fit on a truck to be delivered. While typical townhouses are often two stories high, the new building has an ADU on the ground floor, similar to the way that 19th-century urban townhouses were built with garden apartments under a larger home. Creating two units, rather than a single townhouse, helps make the design more affordable for homebuyers. [Photo: Prep Solutions] Renting out the 660-square-foot ADU can help pay the mortgage for the 2,007-square-foot townhouse upstairs. Families with young children—the target demographic—could also use the lower unit as an in-law apartment for grandparents. (It looks a little like another skinny Pittsburgh-based modular house, from a startup called Module, that’s designed to add an extra story as a family needs more space.) The concept home, dubbed The Picket Fence, was designed after a survey of 10,000 homeowners and renters that began early in the pandemic. The study had three phases, looking at how COVID-19 changed how people thought about their homes. [Photo: Prep Solutions] “Inflation was the number one worry,” says Teri Slavik-Tsuyuki, principal of tst ink, an agency that focuses on consumer insights for developers and homebuilders and helped lead the study. “We learned that homes needed to be more attainable to build and purchase, but also to operate.” The home is designed to be extra energy-efficient, with triple-pane windows, continuous insulation, and heat pumps. The home’s built-in air purification tech is also energy-efficient. In May, when the 100% electric building was completed, the team started studying the energy performance. Over the hot summer, with the indoor temperature set to 72 degrees, the electric bill for the studio was around $40 a month; the townhouse averaged $120. “That’s substantially less than my home in the suburbs, which is about the same size, or actually even a little smaller,” says Steigerwalt. [Photo: Prep Solutions] The survey showed that consumers are also worried about climate change and recognize the link between homes and emissions. By using modular construction in a factory—where materials can be cut precisely and building can be more carefully controlled—the project reduced construction waste by an estimated 90%. The design team also chose materials based both on their carbon footprint and how long they were likely to last before they’d need to be replaced. Because the building is squeezed into an urban lot in an existing neighborhood rather than part of suburban sprawl, it also helps shrink transportation emissions. The design targets millennials, now the largest group of homebuyers, using details from the survey. One of the findings: rather than having a larger number of bedrooms, millennials prefer having extra space in the primary bedroom. “The data showed that was one of the most important rooms in the home for them,” says Ryan White, director of design at Dahlin Architecture, the architecture firm that partnered on the project. “That’s their private personal space. They’re very comfortable sitting there reading a book, watching a movie, looking at Instagram, exercising, or even working in that space.” [Photo: Prep Solutions] The primary bedroom in the townhouse has extra lounge space at the front of the home, with an oversize window to let in as much natural light as possible. It can double as an at-home office. There’s a second bedroom at the back of the home, and another flexible space on the top floor that could be used either as an office or a third bedroom for a child. Another flexible space on the main floor could also double as a bedroom. At the front of the main floor, a family room opens out to a wide, deep porch with a view. Underneath it, the ADU apartment also has its own private porch, something that’s more unusual for rental homes. The team believes that by continuing to refine the design and engineering, the cost of the home could be affordable for families making 120% of the area median income. “The goal is to get these to a point where they could be afforded by the masses,” Steigerwalt says. (The building was listed this week for $930,000, although the developers hope that if the model is produced at scale, it could be closer to $600,000.) [Photo: Prep Solutions]
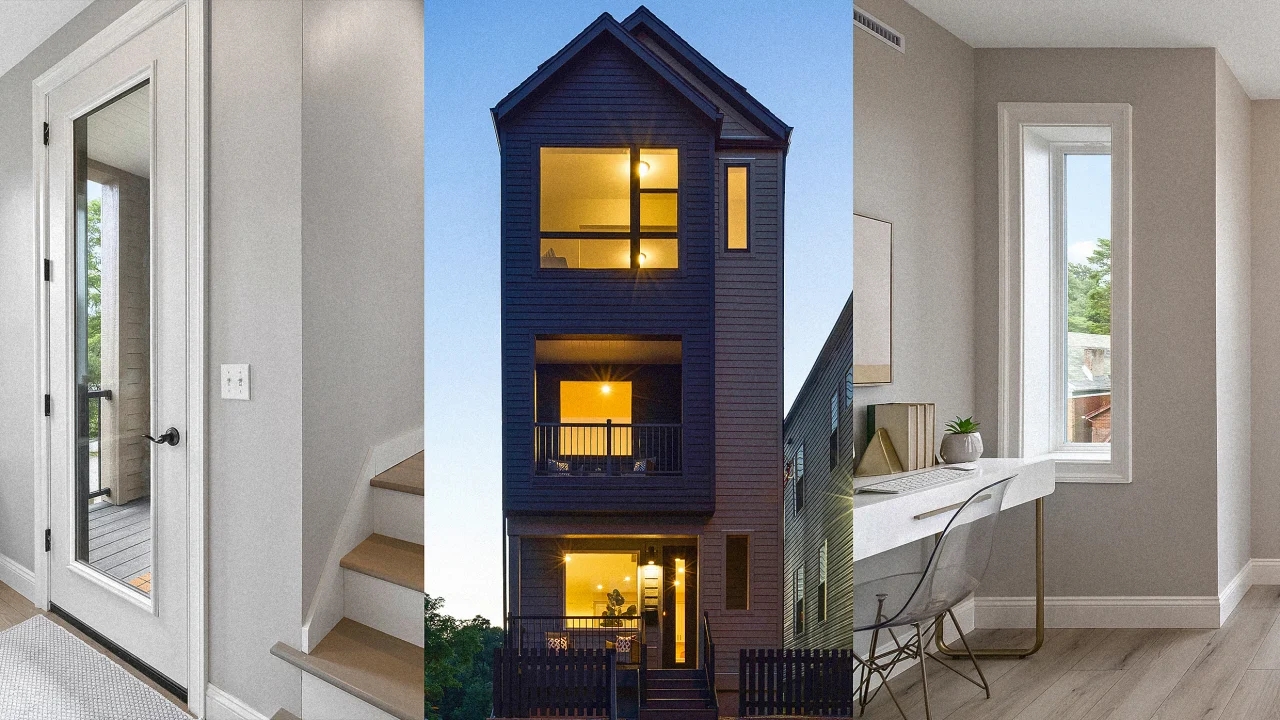
On a narrow lot in Pittsburgh, a new building is three stories tall but only about 16 feet wide.
The shape is based in part on the constraints of the lot—it’s not uncommon for houses in the city to be very narrow. “When you think about Rust Belt cities, there’s a lot of ‘missing teeth’ lots . . . many of these lots in the city of Pittsburgh are 20 feet wide,” says Dennis Steigerwalt, president of the Housing Innovation Alliance, part of a group that built the home as a model for more sustainable, affordable housing.
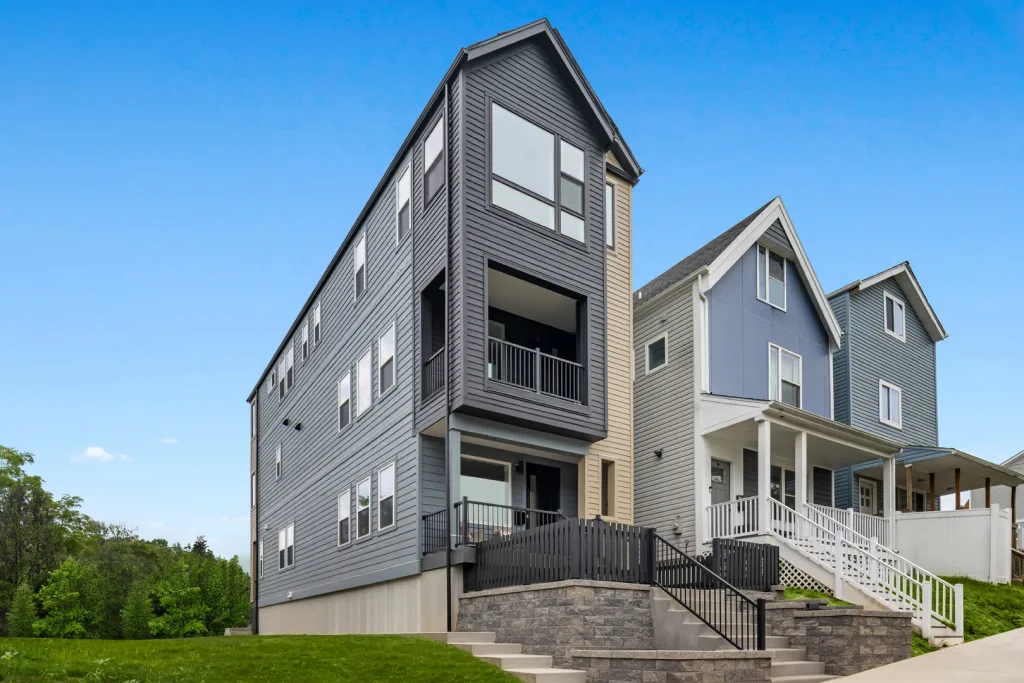
There’s another reason for the size: Because the home was built in a factory, it also meant that each module couldn’t be wider than 16 feet in order to fit on a truck to be delivered.
While typical townhouses are often two stories high, the new building has an ADU on the ground floor, similar to the way that 19th-century urban townhouses were built with garden apartments under a larger home. Creating two units, rather than a single townhouse, helps make the design more affordable for homebuyers.
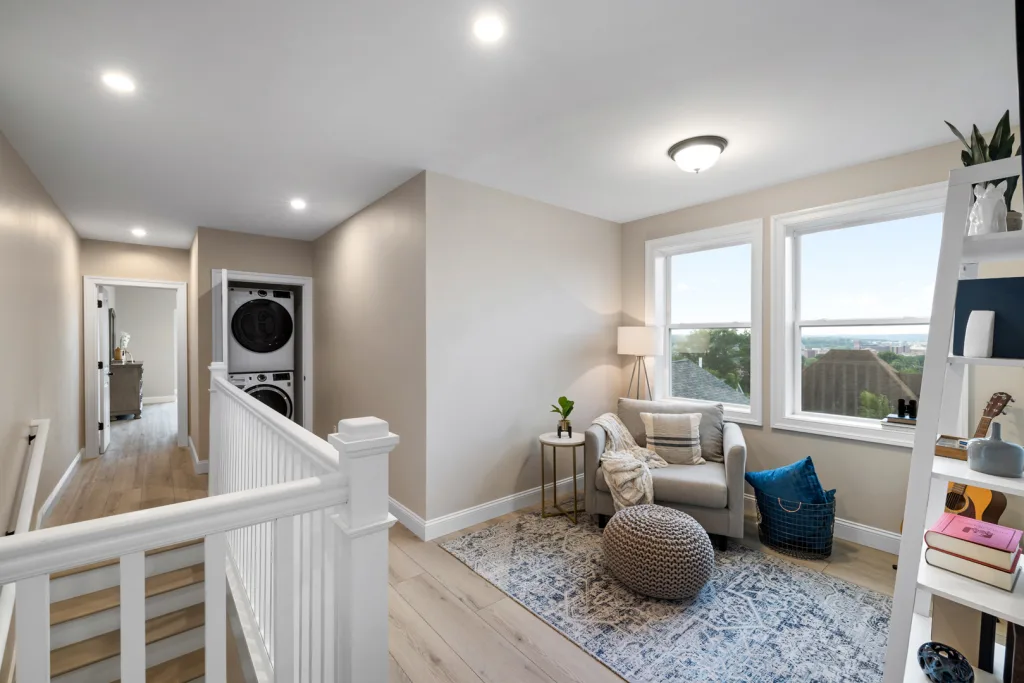
Renting out the 660-square-foot ADU can help pay the mortgage for the 2,007-square-foot townhouse upstairs. Families with young children—the target demographic—could also use the lower unit as an in-law apartment for grandparents. (It looks a little like another skinny Pittsburgh-based modular house, from a startup called Module, that’s designed to add an extra story as a family needs more space.)
The concept home, dubbed The Picket Fence, was designed after a survey of 10,000 homeowners and renters that began early in the pandemic. The study had three phases, looking at how COVID-19 changed how people thought about their homes.
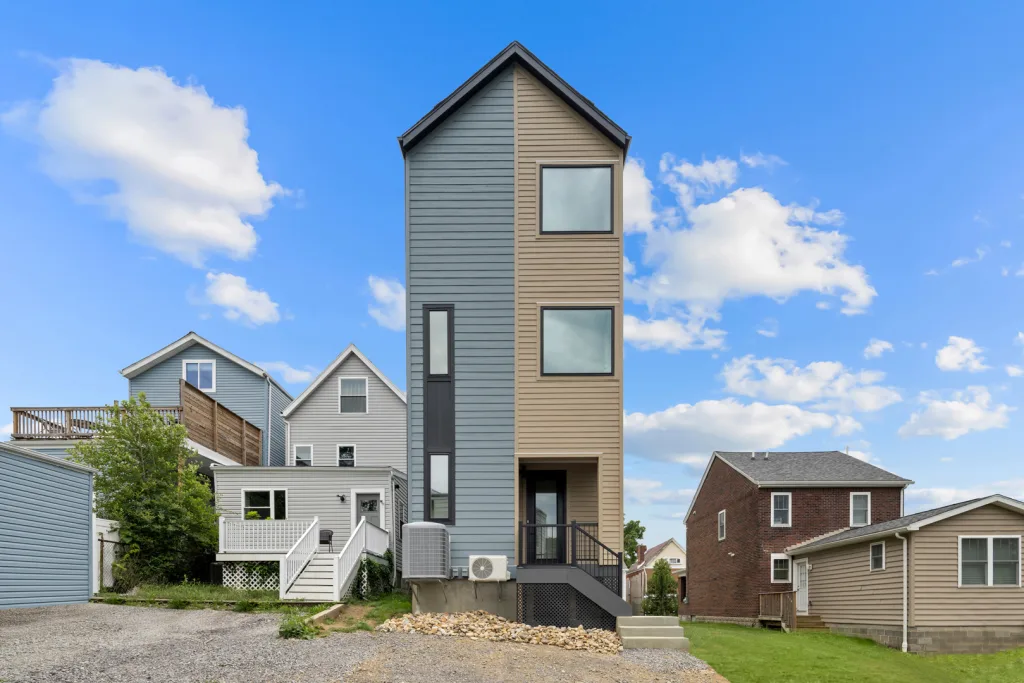
“Inflation was the number one worry,” says Teri Slavik-Tsuyuki, principal of tst ink, an agency that focuses on consumer insights for developers and homebuilders and helped lead the study. “We learned that homes needed to be more attainable to build and purchase, but also to operate.” The home is designed to be extra energy-efficient, with triple-pane windows, continuous insulation, and heat pumps. The home’s built-in air purification tech is also energy-efficient.
In May, when the 100% electric building was completed, the team started studying the energy performance. Over the hot summer, with the indoor temperature set to 72 degrees, the electric bill for the studio was around $40 a month; the townhouse averaged $120. “That’s substantially less than my home in the suburbs, which is about the same size, or actually even a little smaller,” says Steigerwalt.
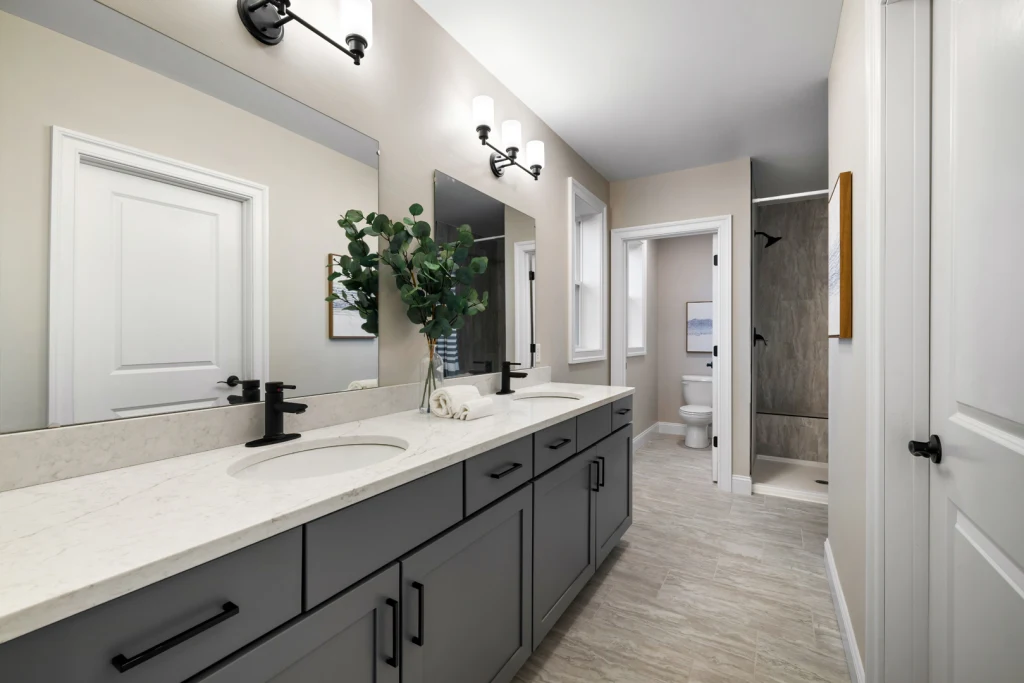
The survey showed that consumers are also worried about climate change and recognize the link between homes and emissions. By using modular construction in a factory—where materials can be cut precisely and building can be more carefully controlled—the project reduced construction waste by an estimated 90%. The design team also chose materials based both on their carbon footprint and how long they were likely to last before they’d need to be replaced. Because the building is squeezed into an urban lot in an existing neighborhood rather than part of suburban sprawl, it also helps shrink transportation emissions.
The design targets millennials, now the largest group of homebuyers, using details from the survey. One of the findings: rather than having a larger number of bedrooms, millennials prefer having extra space in the primary bedroom. “The data showed that was one of the most important rooms in the home for them,” says Ryan White, director of design at Dahlin Architecture, the architecture firm that partnered on the project. “That’s their private personal space. They’re very comfortable sitting there reading a book, watching a movie, looking at Instagram, exercising, or even working in that space.”
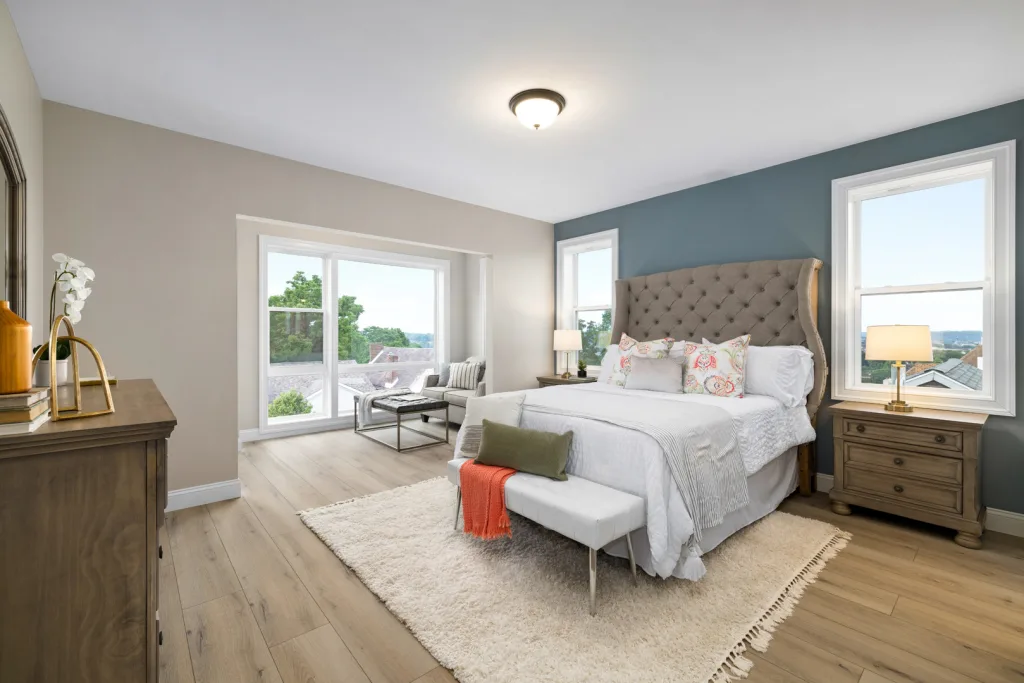
The primary bedroom in the townhouse has extra lounge space at the front of the home, with an oversize window to let in as much natural light as possible. It can double as an at-home office. There’s a second bedroom at the back of the home, and another flexible space on the top floor that could be used either as an office or a third bedroom for a child. Another flexible space on the main floor could also double as a bedroom. At the front of the main floor, a family room opens out to a wide, deep porch with a view. Underneath it, the ADU apartment also has its own private porch, something that’s more unusual for rental homes.
The team believes that by continuing to refine the design and engineering, the cost of the home could be affordable for families making 120% of the area median income. “The goal is to get these to a point where they could be afforded by the masses,” Steigerwalt says. (The building was listed this week for $930,000, although the developers hope that if the model is produced at scale, it could be closer to $600,000.)
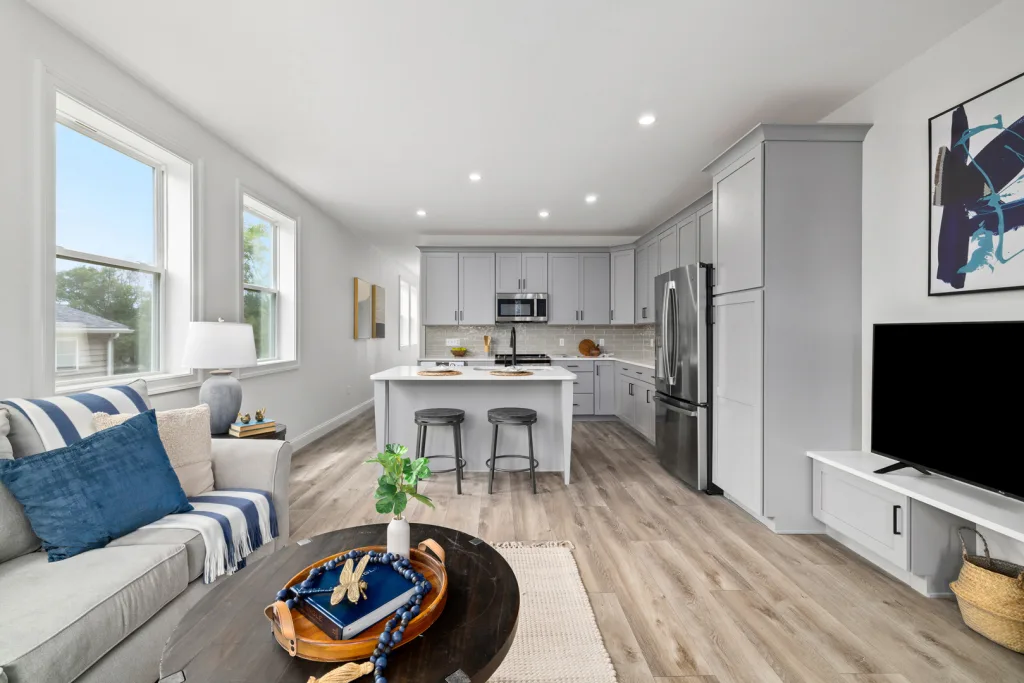
After studying the energy performance over the summer, the home is being showcased to the public and building industry this month. Then the team will continue studying the building, and sharing the learnings with other builders. The Housing Innovation Alliance, a network of more than 2,000 companies focused on residential construction, wants to use the building as a blueprint, says Steigerwalt.
“We see this model as particularly translatable in cities across the industrial Midwest that have desirable urban locations found through these types of vacant lots,” he says. “This is especially true for cities that are reinventing themselves around emerging economic opportunities and delivering a high quality of life at a comparatively lower cost of living.”
It could also be useful in suburbs, he says. The modular design can easily be adapted to differently shaped lots—outside Pittsburgh, for example, the home might be wider, longer, or a different height.