This German startup uses hops to reduce waste from beer and construction
Two students in Munich, sipping beers on their dormitory couch in 2022, chatted about a recent lecture describing the use of banana fibers in Colombia to make sustainable building materials. Wouldn’t it be great, the Technical University of Munich students joked, to do something similar with a local product in Bavaria—perhaps with the waste from the region’s famous hops? The next day, they began researching. Within months, they’d launched a startup called HopfON—a play on Hopfen, the German word for hops—that’s now scaling up from its lab models and pilot project to real-world products. While HopfON’s goal is to reduce waste created by the construction and beer industries by making products that use the leaves, spines, and vines left over from the hops harvest, the Society of Hop Research in the heart of Bavaria is breeding new varieties that reduce the plant’s excess from the beginning. The figures surrounding waste are staggering. More than one-third of all waste generated in the European Union comes from the construction and demolition industry, according to an EU report published in January. And when hops are harvested each fall in Germany’s Hallertau region—the world’s largest hops-growing area that’s about an hour north of Oktoberfest—for every 1 kilogram (2.2 pounds) of material inside the cones that can be used to brew beer, there are 3.5 kilograms (7.7 pounds) of wasted biomass from the rest of the plant. That’s a ratio that’s roughly 20% usable product to 80% waste. Some of the hops waste can be used for fertilizers, and a portion can be sold to biogas plants to produce energy. But the majority is unusable for farmers, who may be forced to rent additional farmland to dump piles of the waste away from their crops. The piles can ferment and emit greenhouse gases—and sometimes catch fire. “We saw a huge potential in sourcing locally and also using a waste stream that was neglected by basically most people,” HopfON entrepreneur Mauricio Fleischer Acuña told the Associated Press. HopfON seeks to reduce the construction industry’s waste, and its planet-warming emissions, by limiting the need for finite resources through hops-made products. The startup has also launched a circular model where customers can return their products to be remade into new materials. During the fall harvest, the team takes the fresh material from farms and dries it immediately, Fleischer Acuña said, then removes any impurities and recyclable metals. It’s chopped up and separated out for a patent-pending process that uses binding agents already in the plant to turn the biomass into products like acoustic panels, thermal insulation and building boards. A coworking space in the southwestern German city of Mannheim was the startup’s first customer for the acoustic panels. A future plan is to make drywall alternatives. Fleischer Acuña and his partners—Marlene Stechl and Thomas Rojas Sonderegger, the two students in the university dorm—also plan to widen their business to use other organic materials and will eventually change their name from HopfON to Onmatter. The trio is not the only group in Bavaria seeking to solve this problem. At the Society of Hop Research in Hüll, researchers have developed new varieties of hops that are more sustainable and produce less waste. Managing Director Walter König says the new varieties mean that for every 1 kilogram (2.2 pounds) of cones, there are just 1.2 to 1.4 kilograms (2.6 to 3.1 pounds) of waste. Perhaps most importantly, König said the research did not sacrifice the quality of the hops—meaning they ultimately retained the traditional taste that brewers, and beer lovers, want. “It’s a very sophisticated thing to bring them all together for a new variety that smells good and that fits to the beers that we need,” he added. —By Stefanie Dazio, Associated Press Pietro De Cristofaro contributed to this report. Associated Press climate and environmental coverage receives support from several private foundations. See more about AP’s climate initiative here. The AP is solely responsible for all content.
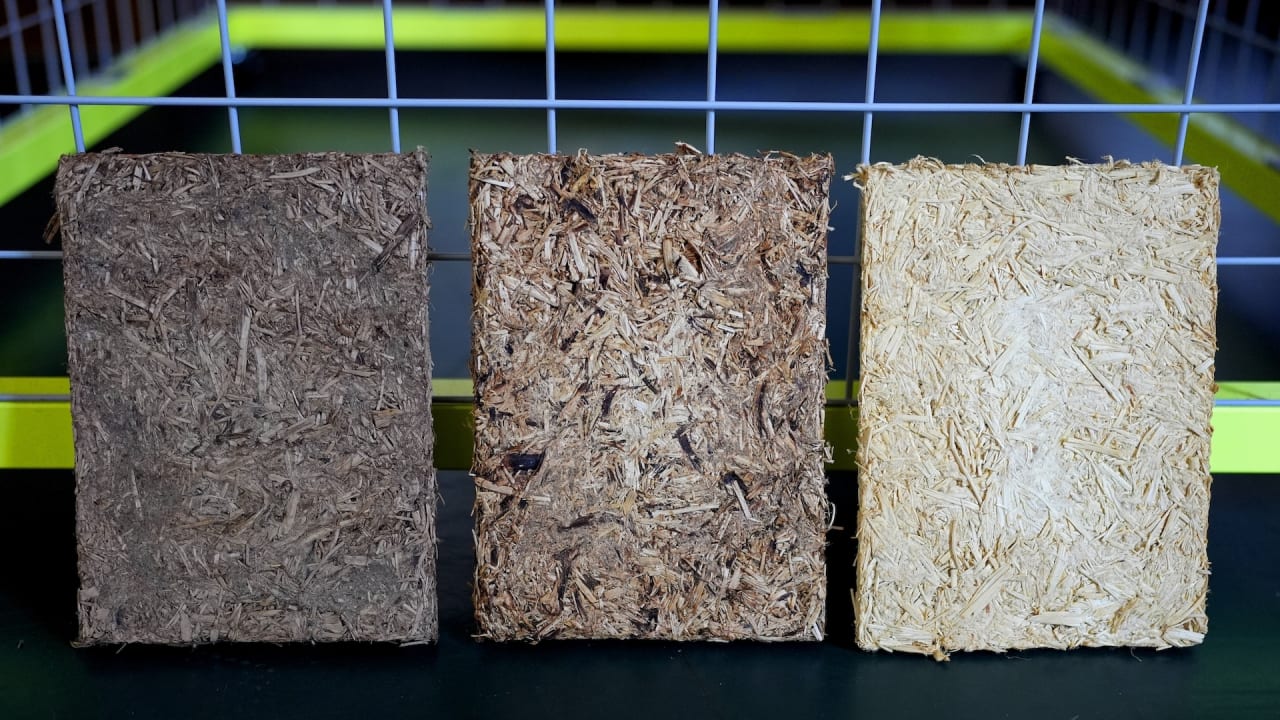
Two students in Munich, sipping beers on their dormitory couch in 2022, chatted about a recent lecture describing the use of banana fibers in Colombia to make sustainable building materials.
Wouldn’t it be great, the Technical University of Munich students joked, to do something similar with a local product in Bavaria—perhaps with the waste from the region’s famous hops?
The next day, they began researching. Within months, they’d launched a startup called HopfON—a play on Hopfen, the German word for hops—that’s now scaling up from its lab models and pilot project to real-world products.
While HopfON’s goal is to reduce waste created by the construction and beer industries by making products that use the leaves, spines, and vines left over from the hops harvest, the Society of Hop Research in the heart of Bavaria is breeding new varieties that reduce the plant’s excess from the beginning.
The figures surrounding waste are staggering. More than one-third of all waste generated in the European Union comes from the construction and demolition industry, according to an EU report published in January.
And when hops are harvested each fall in Germany’s Hallertau region—the world’s largest hops-growing area that’s about an hour north of Oktoberfest—for every 1 kilogram (2.2 pounds) of material inside the cones that can be used to brew beer, there are 3.5 kilograms (7.7 pounds) of wasted biomass from the rest of the plant. That’s a ratio that’s roughly 20% usable product to 80% waste.
Some of the hops waste can be used for fertilizers, and a portion can be sold to biogas plants to produce energy. But the majority is unusable for farmers, who may be forced to rent additional farmland to dump piles of the waste away from their crops. The piles can ferment and emit greenhouse gases—and sometimes catch fire.
“We saw a huge potential in sourcing locally and also using a waste stream that was neglected by basically most people,” HopfON entrepreneur Mauricio Fleischer Acuña told the Associated Press.
HopfON seeks to reduce the construction industry’s waste, and its planet-warming emissions, by limiting the need for finite resources through hops-made products. The startup has also launched a circular model where customers can return their products to be remade into new materials.
During the fall harvest, the team takes the fresh material from farms and dries it immediately, Fleischer Acuña said, then removes any impurities and recyclable metals. It’s chopped up and separated out for a patent-pending process that uses binding agents already in the plant to turn the biomass into products like acoustic panels, thermal insulation and building boards.
A coworking space in the southwestern German city of Mannheim was the startup’s first customer for the acoustic panels. A future plan is to make drywall alternatives.
Fleischer Acuña and his partners—Marlene Stechl and Thomas Rojas Sonderegger, the two students in the university dorm—also plan to widen their business to use other organic materials and will eventually change their name from HopfON to Onmatter.
The trio is not the only group in Bavaria seeking to solve this problem. At the Society of Hop Research in Hüll, researchers have developed new varieties of hops that are more sustainable and produce less waste. Managing Director Walter König says the new varieties mean that for every 1 kilogram (2.2 pounds) of cones, there are just 1.2 to 1.4 kilograms (2.6 to 3.1 pounds) of waste.
Perhaps most importantly, König said the research did not sacrifice the quality of the hops—meaning they ultimately retained the traditional taste that brewers, and beer lovers, want.
“It’s a very sophisticated thing to bring them all together for a new variety that smells good and that fits to the beers that we need,” he added.
—By Stefanie Dazio, Associated Press
Pietro De Cristofaro contributed to this report.
Associated Press climate and environmental coverage receives support from several private foundations. See more about AP’s climate initiative here. The AP is solely responsible for all content.